EV Systems Architecture
Designing R&D circuits and firmware for the next generation of electric vehicles.
Role
Embedded Systems Engineer
Location
Austin, Texas
Tools
KiCad, Beagle Board, Arduino, Linux, C / C++, Python, Node.js, JavaScript, Texas Instruments, Nordic, Solidworks, Draw.io, Adafruit, Git
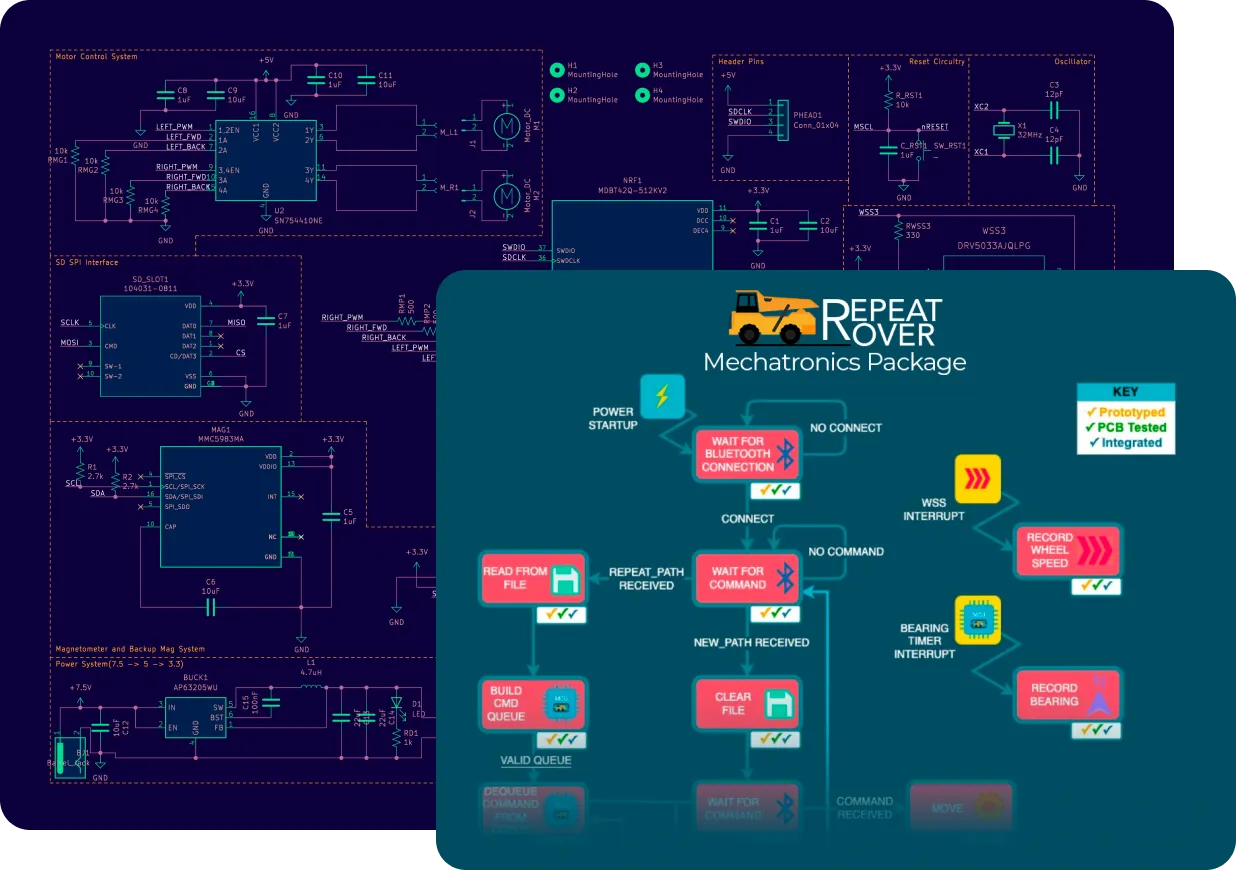
Premise
Note: To comply with the company's Non-Disclosure Agreement, only information which is in the public domain or common practice has been given in this report. This report is in the context of my work for a Industry 4.0 R&D company and research projects conducted at Purdue University. As an Embedded Systems Engineer at this company, I had the pleasure of working on a team with the goal of creating advanced gear systems.
Challenge
The electric vehicle industry is a fast evolving one. As the industry continues to grow, I have had the pleasure of completing several projects in electric vehicle embedded systems technology, combining both firmware and electrical design. Two of these projects related to distinct yet interconnected domains: the design of an innovative electrical circuit and firmware for a motorcycle with a mechanically modernized transmission system, and the creation of a rover capable of performing repetitive tasks in various repeat process environments. Both projects required cutting-edge solutions that would set new standards in efficiency, performance, and adaptability.
Solution
Solutions for these projects involved a holistic approach that seamlessly integrated various technologies. For the motorcycle, a state-of-the-art EV Systems Architecture was designed, optimized for telemetry and efficiency, and integrated with the modern transmission system. The rover required a modular and scalable embedded system, equipped with advanced algorithms to enable autonomous learning and task optimization. The image to the left shows the mechatronics processes for the Repeat Rover project.
Development Tools
Design and Development Choices
Both projects involved coinciding sets of technology such as the KiCAD electric design suite, Solidworks for modeling custom mechanical components, and C++ as the basic language for providing microcontroller instructions. While the motorcycle project used prototyping controllers such as Arduino and Beagle Bone, the rover project was controlled by a Nordic nRF52 chip with custom firmware mounted on a custom PCB. The motorcycle interfaced with custom hardware to interact with the CANBUS, read real-time wheel speed data from the ABS system, and assert motor shifting with asynchronous motors. The rover, on the other hand, used a custom set of reluctors and hall effect sensors, an accelerometer, and bluetooth to recieve and compute instructions. Realtime telemetry and testing UI were programmed with Node.js and JavaScript for both projects.
Result
The combined result of both projects demonstrated an advancement in both the automotive and robotics industries. The data collected from the motorcycle with a modernized transmission system proved significant growth in the future of the EV industry, setting new standards in performance. Simultaneously, the rover's intelligent design enabled it to function in repeat process environments, showcasing the potential for further innovation in automation and robotics.
